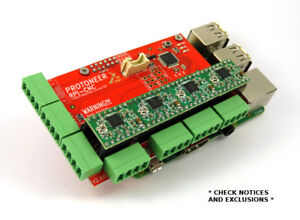
Some stepper drivers will automatically generate the step sequence. You only need to import the pigpio module if you are using its features. That seems unlikely from the information provided so far.
Unlike conventional electric motors, stepper motors allow you to rotate the axis in precise increments. Your focus in interfacing stepper motors with RPi is the GPIO pins that can be found in number of 2×header pins including SPI, I2C, serial UART, 3. These small stepper motors are available on ebay for £3. Notes, schematics, code, updates and other resources are. Unlike a normal motor , stepper motors can control the steps individually and can therefore detect the exact position.
The motor is quite low power and suffers less from the surges in current than DC motors and servos (which use DC motors). The driver board has 5v -12v input: Will supplying more than 5v to the driver board damage my motor ? The PI is one of most trusted project development platforms out there now. Stepper motor driver board.

In addition to stepper motors , there are also small and cheap servo motors. Unlike stepper motors , servomotors can be controlled with a single GPIO. BJY-is a small 5V stepper motor with gear train. It is cheap and easy to get. Is there a detailed tutorial (schematic, part numbers) to help make stepper motor drivers controlled by a raspberry pi ? This little chip can drive either two DC motors or one stepper motor.
Also, the chip is only $5. Motor power supply (e.g. battery). This is the actual code that drives the motor using the GPIO pins. Raspberry Pi ’s GPIOs can be used to control stepper motor rotation.
To do this I am using a language called Python. It comes installed on Raspbian which is a bonus. A simple motor will spin when current is applied to the coils. One is to use an IC specifically designed as a stepper motor controller.
There are TWO pins per motor. I want to move a motor with raspberry pi. WARNING: NO MOTOR SHOULD EVER BE CONNECTED DIRECTLY TO A RASPBERRY PI. FREE Shipping on eligible orders.

Only left in stock - order soon. DC electric motor that divides a full rotation into a number of equal steps. Nevertheless of the design details, from a electronic point of view a stepper motor is formed by many coils.
V for both the Pi and the stepper motors is provided directly from the 5V USB input so no problems with 2. We use the L2motor driver to control the DC motor to move the motor forward or backward. This offers a convenient way of manipulating the outputs without moving the stepper motor. The above set of code applies to running stepper motor 1. Branch: master New pull request Find file Clone or download Clone with HTTPS Use Git or checkout with SVN using the web URL. Below is a picture of the actual board and the accompanying stepper motor and cable and here’s a link to the LC Tech page about the board. It was a bit of a mission getting this working, so I thought others might benefit from a tutorial.
One such method is presented here. In this project I used GPIO pins of the raspberry pi to control the. Actually there is no need to explain more about stepper motors than that video does:. I picked up a 3-axis beefy NEMA-stepper kit from ebay for around $240. By energizing the coils in the right order, the motor is driven round.
PWM (Pulse Width Modulation) is a method used for getting variable voltage out of constant power source. This small reduction 5-wire “28BYJ-48” stepper motor is a fantastic first stepper motor , great for experimenting with your raspberry pi and steppers. This uni-polar motor has a built in mounting plate with two mounting holes, and the motor shaft is flattened so it’s easy to attach stuff with a set screw! The plan was to mount an ultrasonic distance sensor on a stepper motor and have it scan the room drawing a picture of the room as it went.
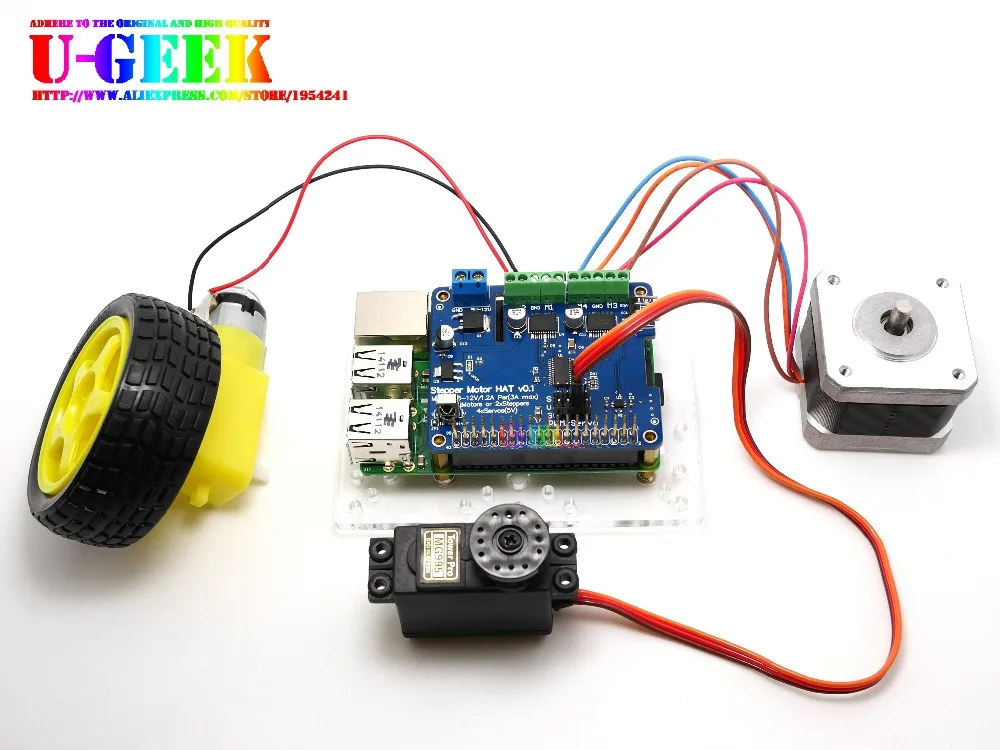
It looks like the L293D cannot operate at 3. Are you driving a unipolar or bipolar stepper motor ? PWM driver chip onboard to both control motor direction and speed. Well I think this is about as good as it will get. A typical H-Bridge module I am using here is an L298N Dual H-Bridge DC motor driver module. Check out our detailed tutorial for tons of info including schematics, wiring diagrams, python libraries and example walkthroughs.
You can get more information about this module here. The mAh the stepper needs to turn are too high for. This board can control a DC motor or stepper motor. Pin „-“ wird an Pin (GND) angeschlossen.
Damit steht die Verkabelung auch schon.
Hiç yorum yok:
Yorum Gönder
Not: Yalnızca bu blogun üyesi yorum gönderebilir.